Surface Finish and treatment
Discover the excellence of our finishes and surface treatments. Reveal the potential of your creations with our expertise.
- All uploaded files are secure
Powder coating
Discover the power of powder coating with LaserSeven! Powder coating, also known as
thermocoating, is a surface coating process where a polymer powder is applied to an object and then
heated to allow the powder to melt and form a durable coating.
Whether it’s sheet metal parts, tubes, or machined components, this process provides corrosion
resistance and a lasting aesthetic finish. Enhance the quality of your metal parts with our custom
powder coating service.
Let us know your needs to tailor a remarkable solution!
Anodizing
Transform the durability and aesthetics of your aluminum parts with our anodization service!
Anodization is an electrochemical process that forms a protective oxide layer on the surface of a metal
material, typically aluminum. This surface treatment imparts enhanced properties such as corrosion
resistance, increased hardness, and improved adhesion for dyes or sealing agents.
Anodization is commonly used in various sectors, including aerospace, automotive, and electronics.
Whether you need a glossy, matte, or colored finish, our experienced team can meet your specific
requirements.
Enhance your pieces with LaserSeven, the anodization specialist.
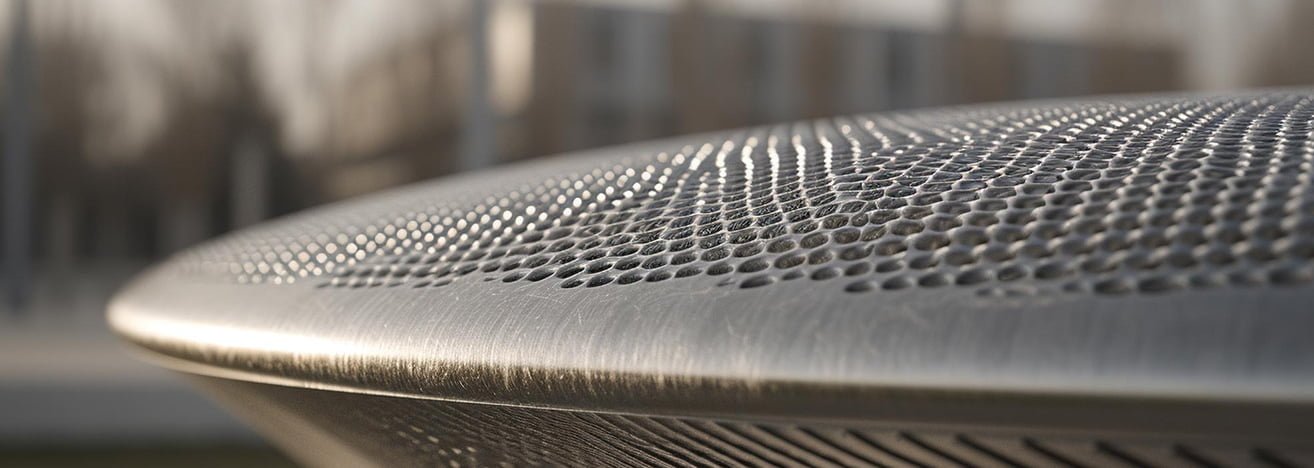
Tempering
Enhance the strength of your metal parts with our quenching service!
Quenching is a heat treatment process commonly used to enhance the mechanical properties of
metals. It involves heating the material to a high temperature, followed by rapid cooling in a medium
such as water or oil. This rapid cooling hardens the material by producing a tougher crystalline
structure.
The quenching process can be applied to various types of metals, including steel, aluminum, and
copper.
It’s important to note that quenching is often followed by a tempering process, where the material is
reheated to a lower temperature to reduce the brittleness induced by quenching while maintaining
the desired hardness.
Provide your metal parts with the essential strength to successfully meet any challenge!
Hot-dip galvanizing
Explore the benefits of hot-dip galvanizing with LaserSeven!
Hot-dip galvanizing is a metal coating process that provides robust corrosion protection to steel
products. Immersed in the zinc bath, steel reacts with zinc to form alloy layers, including an outer layer
of pure zinc and intermediate layers of zinc-iron. These layers create a physical and chemical barrier
against corrosive elements.
After immersion, the galvanized object is lifted for excess zinc drainage, followed by air cooling, and
then subjected to finishing processes.
The advantages of hot-dip galvanizing include excellent corrosion resistance, increased durability,
comprehensive surface protection, and the ability to galvanize complex structures.
Widely used in various industries such as construction, equipment manufacturing, infrastructure, and
naval applications, this process has a proven ability to extend the lifespan of steel products.
Let’s start a new project today
Electro-galvanizing
Electro-galvanizing, or cold galvanizing, is a metal coating process that employs electrolysis to deposit
a thin layer of zinc onto a metal surface. Before the procedure begins, the metal surface is prepared
by removing contaminants. Submerged in an electrolytic bath, the object undergoes electrolysis
where a potential difference causes the deposition of zinc ions onto the base metal surface, forming
a uniform and adherent zinc layer.
Once the zinc layer is formed, finishes can be applied to meet final specifications.
Electrolytic galvanizing is valued for its ability to provide corrosion protection while ensuring a fine
and uniform zinc coating.
Feel free to contact us for more information on our galvanizing services.
Cataphoresis
Cataphoresis, also known as electrophoretic coating, is a coating process used to apply a uniform
layer of paint or resin to metal surfaces.
Prior to the process, the metal surface is prepared and then immersed in a cataphoresis bath
containing an electrolytic solution. Under the influence of an electric field, charged particles move
towards the surface of the object, creating an adherent and uniform coating. The part is
subsequently baked to cure the coating.
Cataphoresis provides effective corrosion protection, uniform application even on complex shapes,
and is utilized in various sectors, including the automotive industry, to coat metal parts requiring
aesthetic finishing and corrosion resistance.